Control valves play a crucial role in many industrial processes, and their proper operation is essential for the smooth functioning of these processes. However, control valves are prone to failure, which can lead to costly downtime and even safety hazards. In this blog post, we will discuss the basic principles of control valves and actuators and the various failure modes that can occur in control valves.
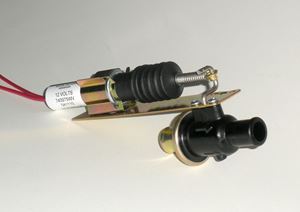
Basic Principles of Control Valves and Actuators:
Control valves are devices that regulate the flow of fluids or gases in industrial processes. They come in various sizes and designs and can be operated manually or automatically. Control valves consist of two main parts: the valve body and the actuator. The valve body is the part that controls the flow of fluid, while the actuator is the part that moves the valve body to adjust the flow.
Actuators are devices that convert energy into motion. In control valves, the actuator is used to move the valve body to regulate the flow of fluid. Actuators come in various types, including electric, pneumatic, and hydraulic. Each actuator type has its advantages and disadvantages, and the choice depends on the specific application requirements.
Valve Failure Modes:
Control valves can fail due to various reasons, including mechanical, electrical, or environmental factors. Here are some common failure modes in control valves:
1. Sticking: Sticking occurs when the valve body gets stuck in a position, leading to improper flow regulation. Sticking can occur due to mechanical or environmental factors, such as corrosion or debris buildup.
2. Leakage: Leakage occurs when fluid escapes through the valve body, leading to a loss of control. Leakage can occur due to valve body damage, improper installation, or wear and tear.
3. Actuator Failure: Actuator failure occurs when the actuator fails to move the valve body, leading to improper flow regulation. Actuator failure can occur due to electrical or mechanical issues, such as wiring damage or motor failure.
4. Calibration Issues: Calibration issues occur when the valve body does not move to the desired position, leading to improper flow regulation. Calibration issues can occur due to electrical or mechanical issues, such as sensor errors or improper adjustment.
Conclusion:
Control valves are essential components in many industrial processes, and their proper operation is essential for the smooth functioning of these processes. However, control valves are prone to failure due to various reasons, such as mechanical, electrical, or environmental factors. Regular maintenance and proper installation can help prevent valve failure and ensure the smooth functioning of industrial processes. Our automation textbook (name removed) provides detailed information on the basic principles of control valves and actuators and various failure modes that can occur in control valves.